Home | Regulations & Compliance | Criticality & Circularity
Criticality & Circularity
Criticality
Antimony is recognized as a critical raw material/mineral in the EU, the US, Japan and Australia. The criticality criteria may vary across these lists, but is globally defined as:
- a high reliance on imports (risk of supply shortage)
- limited substitution options
- an essential function in the manufacture of products which are key to the regional economy and/or national security
The criticality implies not only a high value, but also a high dependence on Antimony, which may be further complicated by the imposition of over-conservative EHS requirements.
i2a works towards evidence-based decision-making to ensure that the use of Antimony faces the least number of irrelevant and/or inapplicable regulatory obstacles as possible.
Circularity
Antimony (Sb) is used in a number of applications and can be found in a number of end-of-life or waste materials, including more particularly:
- Lead (Pb) products (in which Sb had been added to strengthen this naturally soft metal), and
- Polymers (in which traces of Sb can remain following its use as polymerization catalyst, or in which it was added in relatively higher concentrations to serve as flame retardant synergist).
The recycling of Sb contained in Pb-based products takes place as part of the existing highly efficient recycling loop for such Pb-based products. The continued safe use and recycling of Pb hence also ensures that the critical Sb is retained on the market for future use in that value chain.
The recycling of Sb in polymers is less established to date. As regards polyethylene terephthalate (PET), the traces of Sb contained in that polymer following its function as catalyst remains in the PET recycling loop, which constitutes the most circular polymer type to date, thanks to the existence of comparably accessible and affordable collection, sorting and recycling techniques.
As regards the Sb contained in other thermoplastics such as High Impact Polystyrene (HIPS) and Acrylonitrile butadiene styrene (ABS), typically used in electronic and electric equipment (EEE), the process to recover Sb can follow a number of routes.
As indicated above, Sb is added to halogenated compounds having a flame retardancy function, in order to decrease the amount of halogen needed, while at the same time increasing the flame retardancy performance without disrupting the other polymer’s performance properties. Depending on the feasibility of the (manual/mechanical) separation of the EEE product, the resulting fraction may be entirely polymeric, or combined with metals used in the EEE. The metal fraction will normally undergo shredding and smelting for the subsequent recovery of copper and precious metals contents. These are typically used in printed circuit boards (PCBs), for example. When smelting the shredded PCBs, the polymer would be used for energy recovery (replacing cokes for 45%, see Umicore trial here). In parallel, the metals contained in the polymer or other parts of the PCB can be recovered via metallurgical techniques in which Pb again, is used as a carrier for all other metals to be recovered. Step by step through the metallurgical process, different metals and metalloids are recovered for reuse.
According to the WEEE Directive, the halogen-containing polymers in the EEE should not be mixed with other polymers in terms of further waste management steps. Interestingly, it is actually the weight of the Sb which enables the legally required separation of halogen-containing polymers from the other polymers. Once the halogen/Sb fraction of the polymer is separated out via density-based sink-flotation and XRF-based optical sorting techniques, it can undergo its own recycling process, in which both the recovery of the halogen and of the Sb are of commercial and environmental interest. This field is currently subject to innovative partnerships such as the Plast2BCleaned EU-funded project (https://plast2bcleaned.eu/), in which the aim is to close three material loops: the polymer; the bromine (Br) fraction; and the Sb fraction. This project intends to overcome two challenges related to the recycling of Br and Sb: the technical feasibility and the economic viability. Indeed, there is a need to achieve the technical separation of high purity materials both in terms of polymeric identity and Sb and Br contents, while ensuring that the process is economically viable compared to that of producing Br, Sb or the flame retardant polymer from primary sources.
Similar projects like CLOSEWEEE (https://cordis.europa.eu/project/id/641747) and NONTOX (http://nontox-project.eu/) are using the CreaSolv® Process technology as dissolution purification process. With this process, the Sb and Br components in the plastic mixture are selectively dissolved in a special solvent formulation. The specific solubility of the polymers allows the recovery of the Sb, the Br and the polymer with high purity.
Without the necessary political and economic frame, the polymer, Sb and Br are taken to incinerators and could be lost for the circular economy. This does not only constitute a suboptimal use of the carbon/energy source contained in the polymer, but also implies that the Sb and Br ending up in the flue dust or bottom ashes of the incinerator, will be locked in road fillings and other long-term constructions from which the access and recovery of these important chemicals would be even more technically and economically challenging. The recovery of Sb from these incinerators’ ‘by-products’ may have a role to play in a transition to a fully circular economy but does currently not seem to be appealing enough.
The excessive regulatory pressure put on Sb and Br constitutes an additional burden to the promising recycling avenues that are being developed. Instead, regulations should target the integrated concept of ‘safe circularity’ and ‘industrial symbiosis’ that would render recycling of critical raw materials such as Sb more attractive to technical experts and investors.
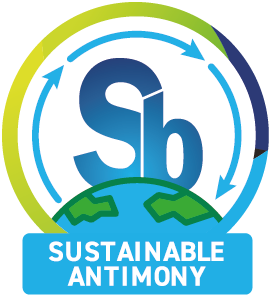